3月7日に東京エレクトロン九州の合志工場へ見学に行ってきました。
半導体はいま世界で最も注目を集めているテーマの一つです。生成AI(人工知能)や自動運転などの最先端IT(情報技術)はアメリカが先行していますが、それを支える半導体の製造装置や素材の産業は日本が強いです。その強みと、コロナによる供給網混乱の教訓、中国の侵攻リスクなどから、半導体そのものの製造で圧倒的地位を築いている台湾企業TSMCの製造拠点の分散先として日本が選ばれており、特にTSMCが工場を構えた熊本は沸きに沸いています。その近くには、ソニーの画像センサー工場、東京エレクトロンの半導体製造装置工場、公立の技術者養成学校などが固まっています。スマホやEV(電気自動車)などに欠かせないエリアと言えるでしょう。
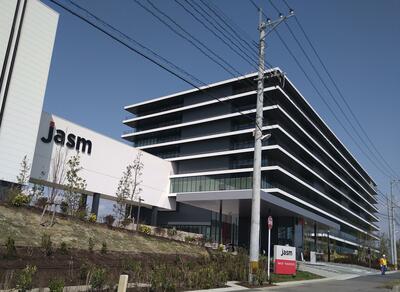
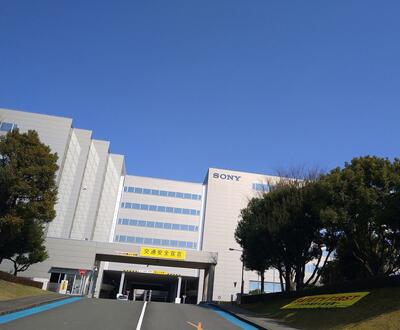
東京エレクトロンの工場と地域の様子を確認すべく、伊井・末山・原嶋・奥の4名で出張してきました。複数名で見学に行くのは“復活”といえるほど、久しぶりのようです。私が入社してからは初めてです。
工場は丘の上にありました。水害はもちろんのこと、丘陵地は比較的地盤が安定している傾向があるとされるので、地震にもある程度対応できそうです。
工場見学は、説明会ののちトレーニングセンターを見て回り、最後に質疑応答という運びでした。少し驚いたのは、同じ時間に見学していたのがほとんど外国(特に中国・台湾系)の投資家だったことで、見学予定時間を1時間超過するほどの熱の入りようでした。台湾の投資家向け説明会では100名を超える参加があったとのこと、さすがの関心の高さです。
トレーニングセンターには歴代の製造装置が並べられており、進化の軌跡が分かるようになっています。昔はウェハーの大型化に合わせて製造装置も大型化させて対応していましたが、新しい世代になるほど同時処理能力と省資源化が進んでいます。機械を縦長にして同時に洗浄などの処理をすることで、工場面積当たりと時間当たりの生産性が向上しており、さらに薬液の必要投入量を減少させることで、ユーザー側の変動費(製造量を増やした時に増えるコスト)を抑えられます。処理回数などに応じて様々なグレードが用意されており、投入する材料費に相当の差異が生じるようです。
製造できる半導体の品質はもちろんですが、生産ラインを止めない信頼をベースに顧客の生産性も高めてきたことでシェアを拡大してきたように見えました。現在取り組んでいることも伺いましたが、製造工程の改良や新領域へのチャレンジなど、持続的成長を再確認できるものでした。